hp indigo
hd printing . implementation . colour . training
We deal with more advanced printing, the one using a wide potential of both printing press and software. We can operate almost all sheet-fed presses and most web-presses from HP series. Marcin worked at R&D, HP Indigo in Israel for more than two years on high quality image printing, that were implemented into production. Operating HP Indigo presses is divided into three stages:
1) concept of file preparation including separations,
2) configuring DFE and press software,
3) print production by press operator.
Each one is of significant importance but understanding their relations is a key to achieve full capabilities of a press. Printing on Indigo machines is a pure pleasure and designing digital work sparks creativity. From one side we are dealing strictly with digital works, but on the other various mechanisms are taken right from offset printing process.
Starting collaboration with a company that has plans to implement or already possess HP press I analyse all stages of production: from file preparations up to final post-press stages. HP Indigo is one of many elements of workflow and in order to use it according to expectations in needs proper set up. When it comes to set up, we can achieve almost anything, biggest limitation comes from ourselves. External help might surprise and for certain it will bring a lot of benefits.
hd printing
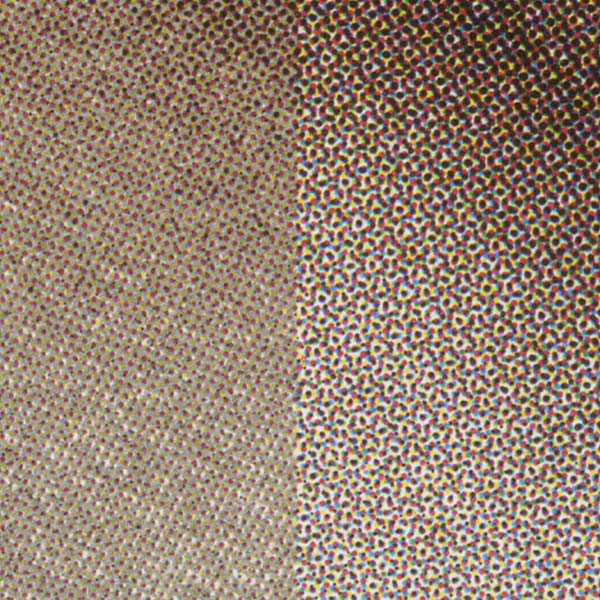
5ch printing:
CMYK + LLk
It’s a process developed by Marcin that’s using grey channel during regular printing process. It requires at least 5-colour press configuration and works with all series 2, 3 and 4 Indigo presses. Enhancing press functionality results in automatic image separation to 5 channels. In order to achieve optimum image quality I choose shade of grey ink carefully for clients individual wishes.
Work results in photographic quality, incomparably more homogenic, natural and sharper. It almost has no rosettes, also is much more robust in light changing situations. With proper file input all B&W images are printed only in duotone, using grey and black ink.
7ch printing
CMYK + Lc + Lm + LLk
This technology is an enhancement of 5ch printing and gives you imaging of maximum quality. Implementation requires understanding of customers wishes and has no universal algorithm. We can prepare setup to work side by side with photo lab, we can also give you maximum quality on certain media and for example greyscale images.
This solution requires full 7-colour configuration.
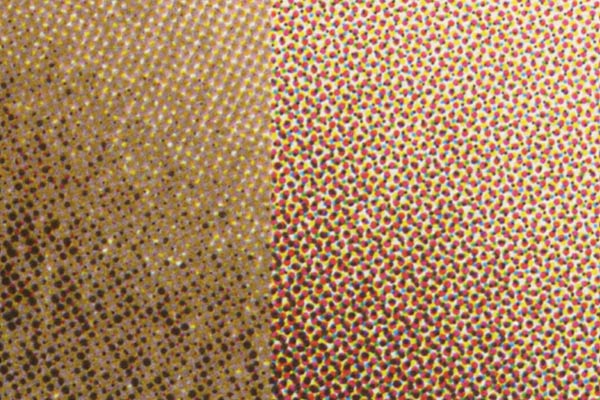
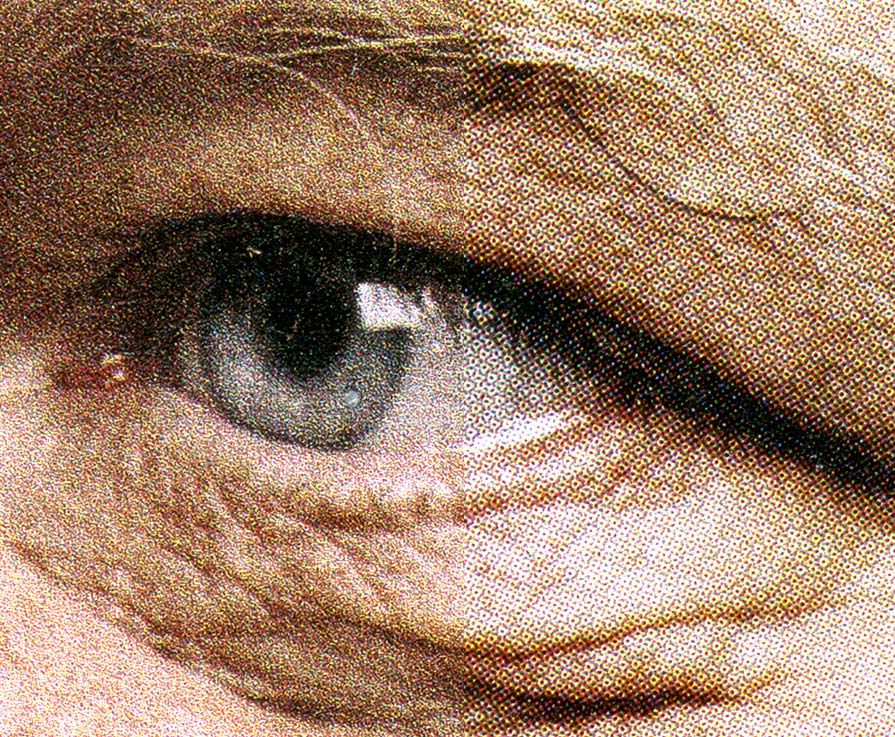
FM & XM screening
On daily basis Indigo press prints with amplitude modulation screening with various linatures. But with proper file preparation you can achieve full colour printing in frequency modulated screening, stochastic and hybrid – also using special inks.
It’s a technique useful in special projects, when we focus on certain enhancing details.
mutlicolour B&W printing
Idea here is simple. To create absolutely perfect looking B&W pictures. We can create it while eliminating chromatic channels (CMY) and introducing halftones – grey inks of various brightness. Sounds uncomplicated, but the catch is in selecting right inks and final separation curves. We can utilise ink that we’re using in 5ch / 7ch printing process as well as create new colour specially for target job and substrate.
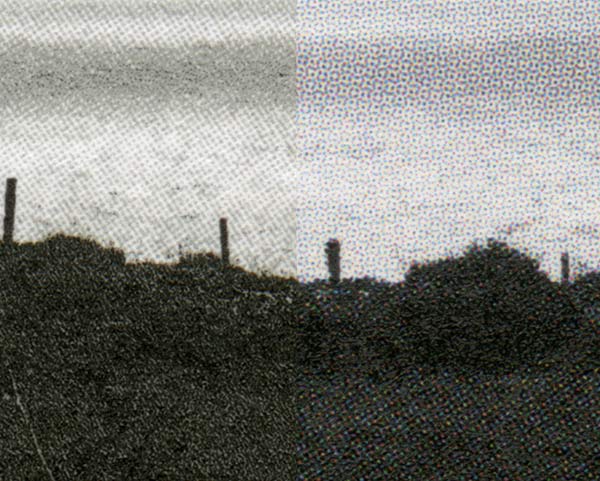
training
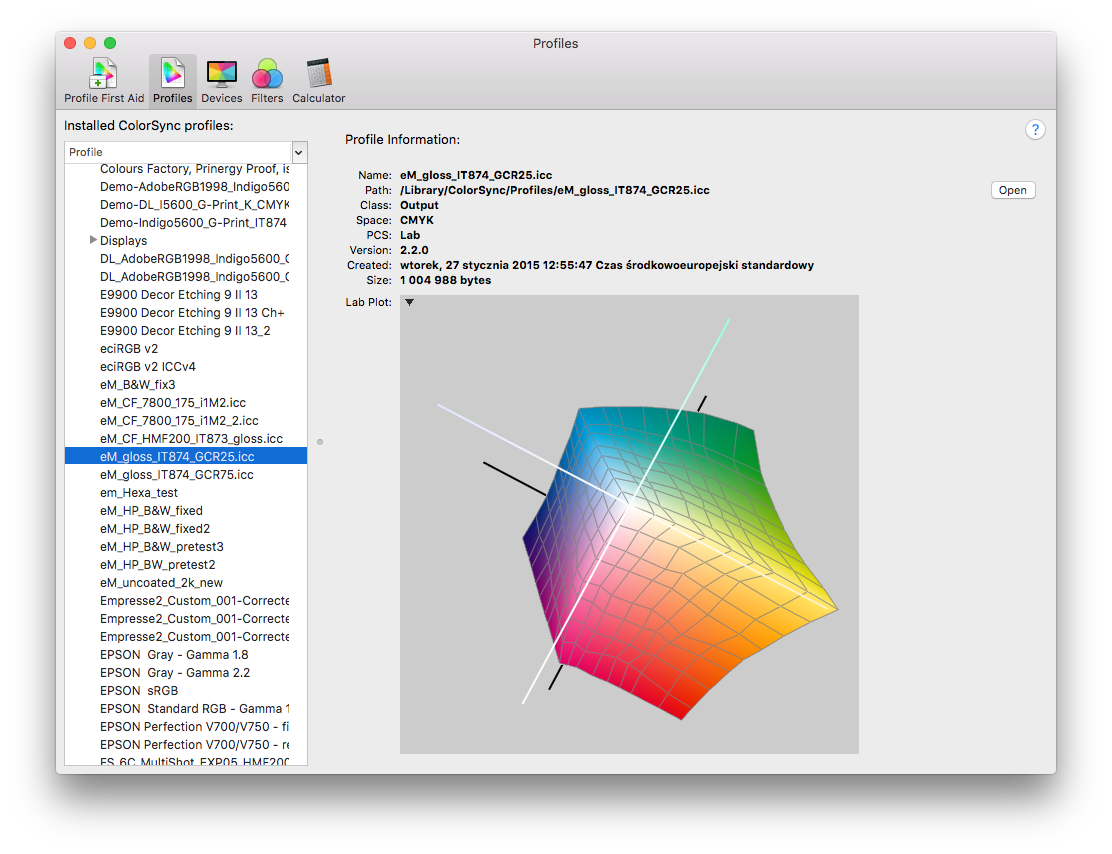
colour
Starting with DFE with explanation colour spaces, through ink definition files, calibration process and it’s options, defining new calibration substrates and it’s selection + determining optical density values… Up to press software and colour control at printing stage, creating ICC profiles… HP Indigo presses gives you a lot of flexibility and with that brings huge possibilities, but in order to choose right path one needs to know most of available ones. Colour will be dismounted into tiny pieces.
DFE and press software
Standard trainings contains technical aspects of press usage as well as basic software elements. But in order to take full advantages of the press you need to analyse such aspects as screening options and their linatures, image sharpening, introducing variable data into files or preparing right file handling paths – ticket templates.
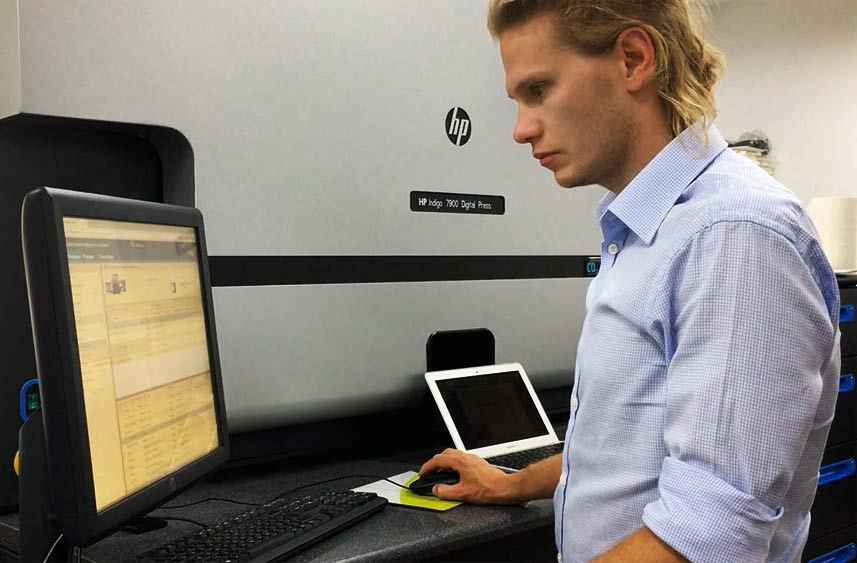
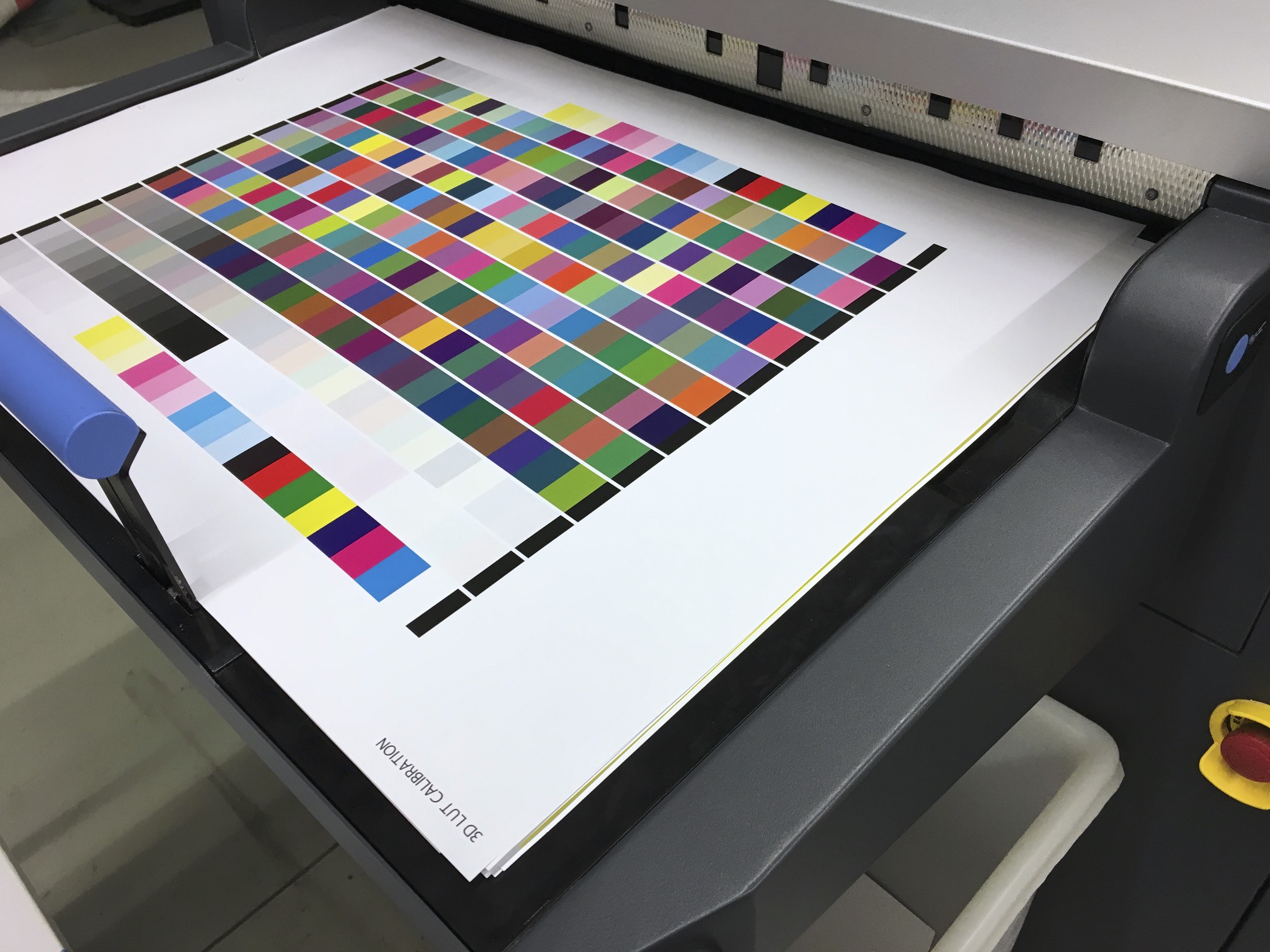
file preparation
It’s very useful part for graphics departments as well as pre press. How to use which colour space: RGB & CMYK? How to implement vector graphics? When to use Pantone inks? Should we change TAC (total area coverage) with uncoated substrates? Those and other questions are worth to answer. But not just simple yes / no, but also with full explanation of a process so that you could answer next question yourself. Thanks to that your files will be using full advantages of a press.
special inks
Besides standard CMYK we can put almost infinite number of inks prepared upon request and also number of special ones like fluorescent or varnish. Each one has it’s own usage requirements involving installation and using. And if we want to properly use our own Ink Mixing Station we should always do it with consideration of print job type and substrate.
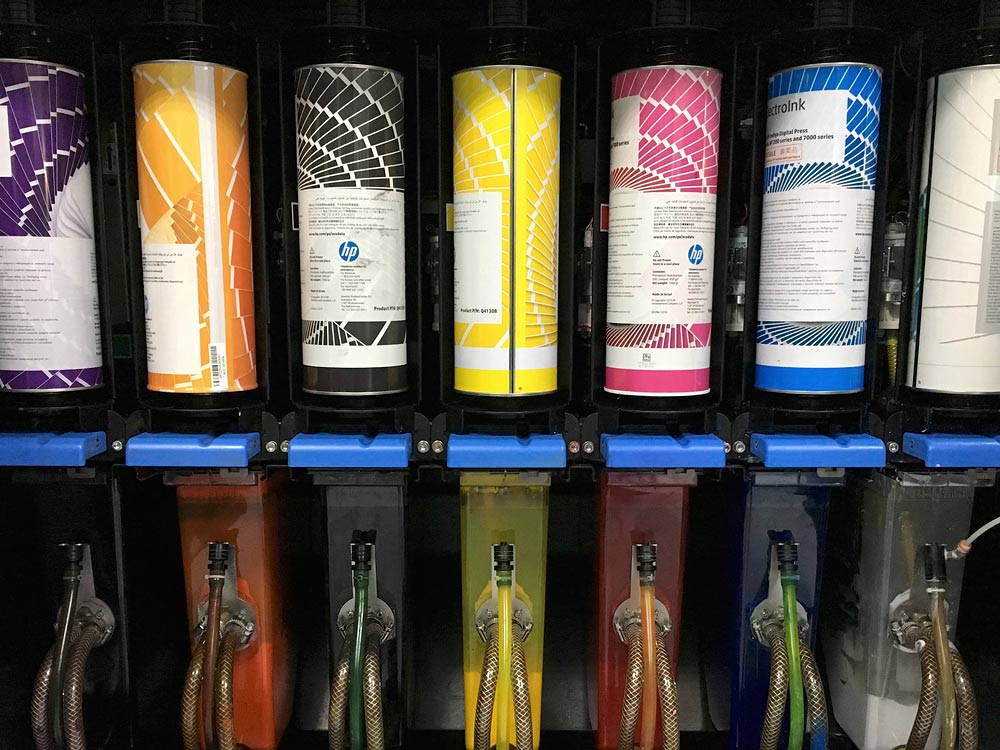