training
print . colour . technology . separations . design . indigo
While being graphic designer you’re looking at a product from computer screen point of view. Well, sooner or later all our visions comes down to digital world. While being a member of production team you’re turning creative concepts to live. Connection between those two world is very real and without proper understanding of other side effect might me random. And not rarely this is what happens.
Below I’m presenting list of training courses for printing industry:
– starting from technical thinking about a product,
creating right design oriented on convenient production,
– preparing accurate separation,
– creating colour profiles for chosen printing environment,
– achieving prints according to clients expectation.

Marcin Dąbrowski
During courses I’m sharing with practical knowledge acquired during competition of several thousand orders that includes design analysis, print production and bindery work. I had lectures on universities (University of Technology in Wrocław and Łódź, Academy of Fine Arts in Łódź), with cooperation and as speaker companies and organisations (Apple, HP, Antalis, DSCOOP, Eizo, Nikon or Allegro among others), and for teams in print houses and design studios. I actively conduct lectures since 2007 in polish and english languages.
creative training
It’s not an education program. Each course is prepared for specific meeting and each one is different. Instead of reading slides I’m using white board for on going illustrations and live examples (well, not entirely live – they do not meow or bark). Below I’m presenting several subjects that are mostly discussed. Even if you’re not seeing exact phrases that you’re looking for – contact me.
colour, colour management, separations
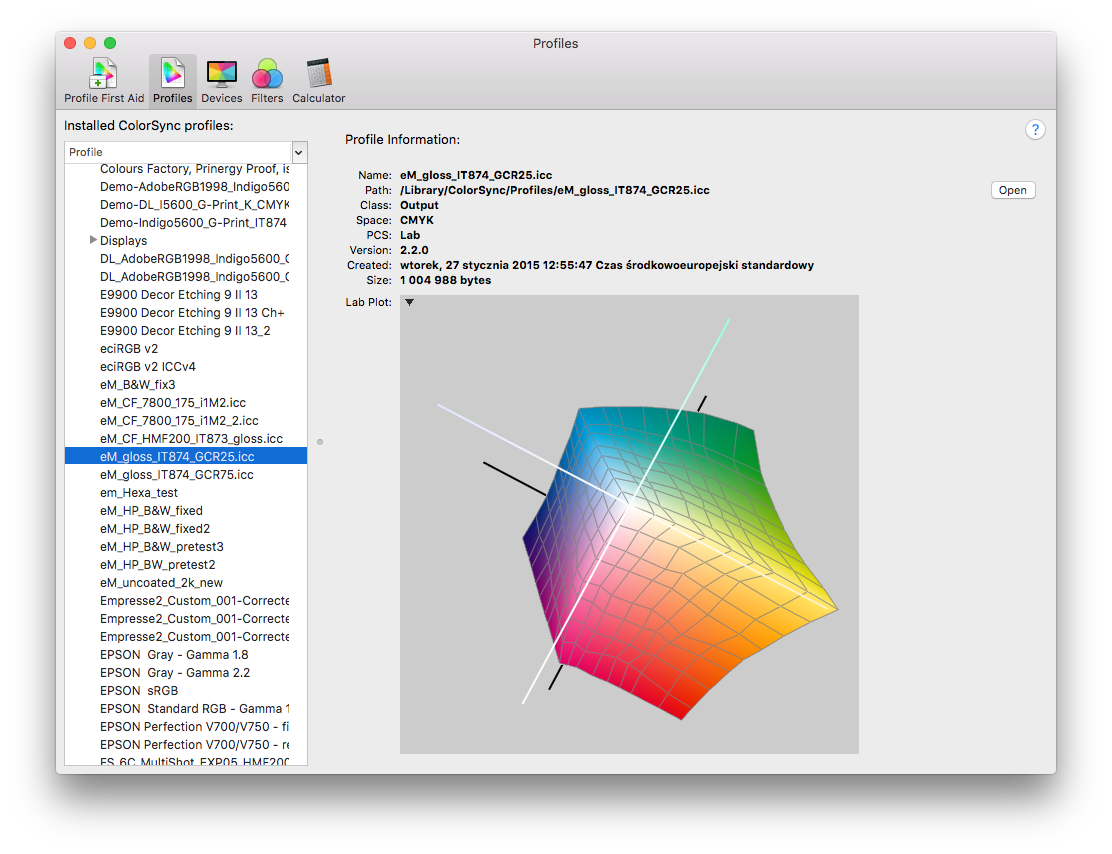
In colour rule is simple – understand it. Just like that. There are no charts, procedures or crazy hundred pages manuals. As an ICC member I believe that this subject is very close to my heart. But not just in theory, practical aspect comes first. We can achieve almost every colour on paper. Question is: what kind of treatment we would have to do first. Deep explanation of this matter I conduct in two stages:
– during training and talks,
– in front of printing press while experiencing live changes.
First part is extremely important in order for us to meet basics and really understand terms like CMYK od Pantone. Practical part is a great way of confirming your knowledge and expand it with new elements. And most important: all fear of unknown will disappear.
During courses we will touch subjects like colour space, basic colours, gamut and it’s change, colour depending on printing technique, calibration, separations, multitone images: duotone, tritone, quadtone.
Suggested course duration is 2-3 days, possibly in 1 day parts. Introduction and theory can be executed at customers site. Practical part requires proper printing equipment so in case there isn’t any at your place you should take under advice additional drive to external site.
design
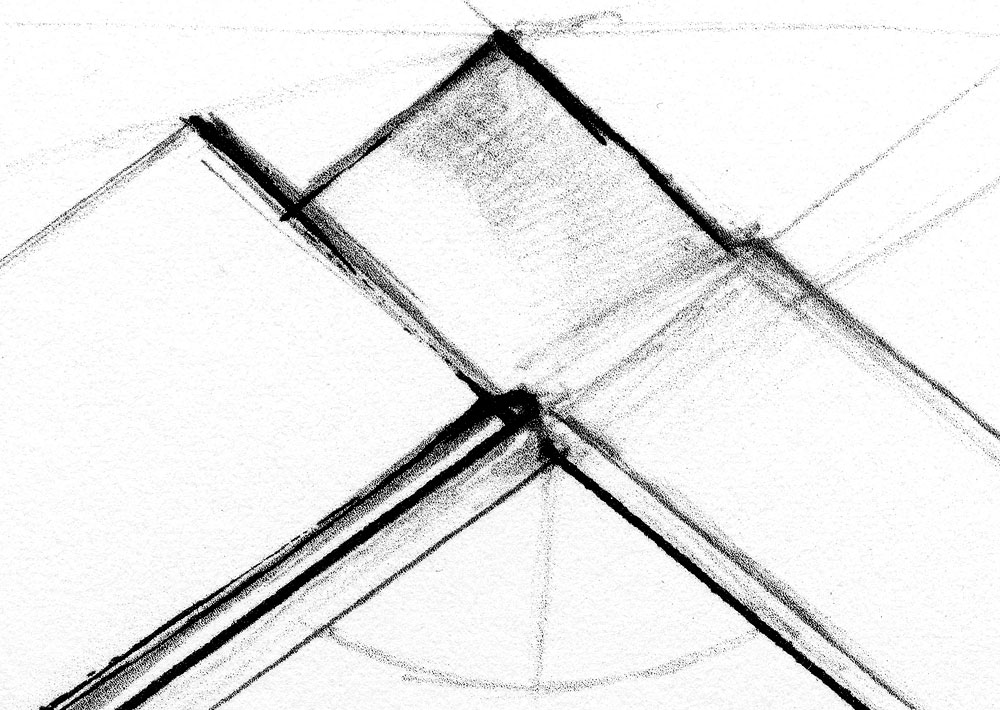
When we’re siting at computer desk, we’re there to transform ideas on screen. But it’s always worth to know what we’re planning to do. That is an effect of what our reasons for this creation was. Effective design requires understanding both substrates and technology that we’re going to use. There are two reasons: to fully embrace possibilities that are in hands reach and to do it right. Corrugated cardboard might be used for both packaging and furnitures, right? This training is meant to open your eyes by explaining technology while describing multiple examples. It’s kind of reverse engineering – creating input design when looking at production unit and analysing possibilities in ready ideas.
This often is one day training at customers site and oriented on specific subject (publishing or cardboard packaging). I gladly show how real production processes looks like: printing, making mockups on cutting table or finishing solutions.
technical training
colour & printing
colour management and spots
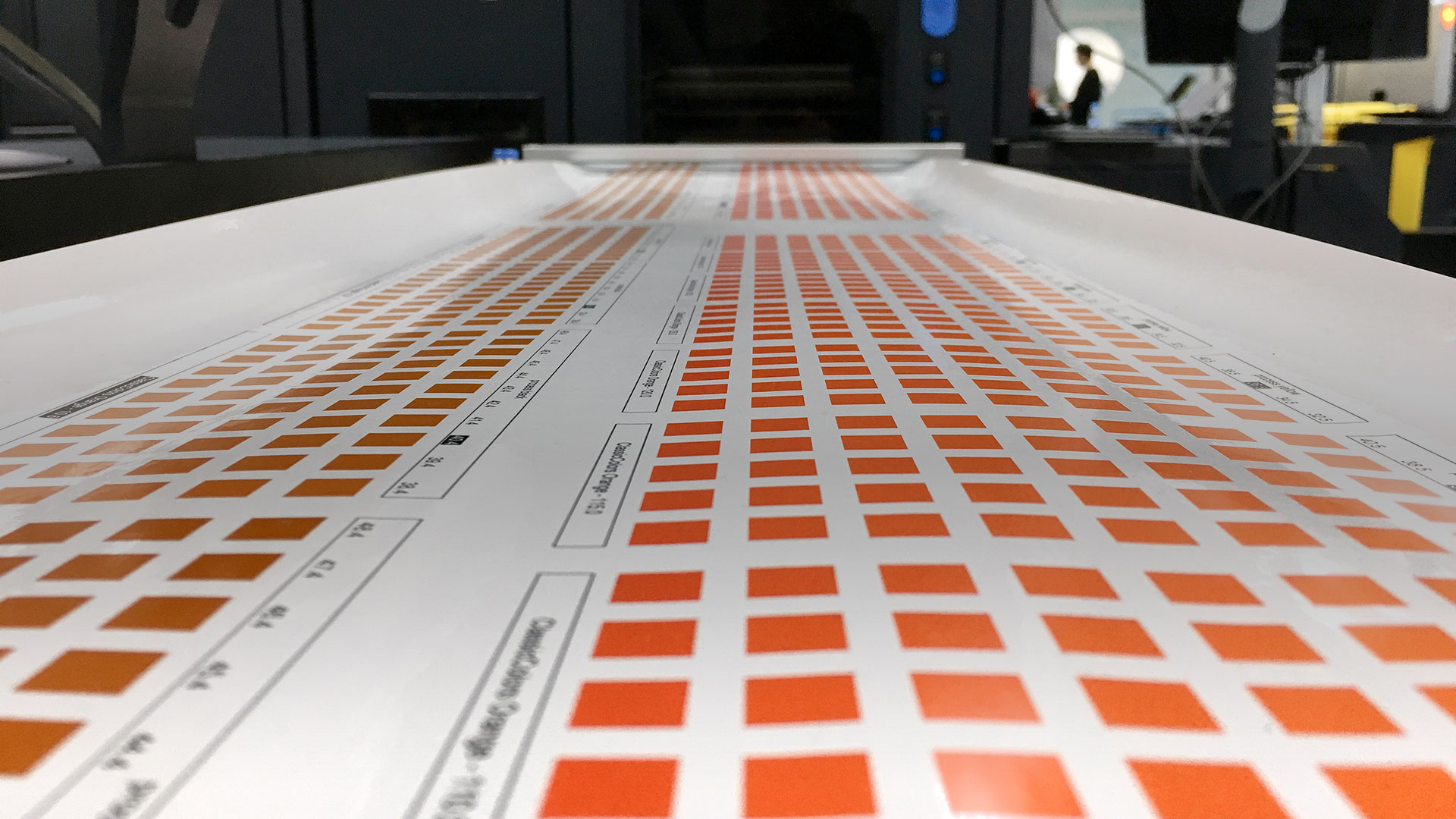
n most cases machines are fully dependable on us – operators – and we decide about their condition and production capabilities. Digital press like Xerox, KonicaMinolta or HP can also be our proofing device. In case of HP Indigo we can emulate offset press in it’s „look and feel“ on various of substrates.
In order to do that we must employ proper colour management policy. And for this certain amount of theoretical knowledge combined with a lot of practical is needed. We must know how to talk about colour and what to expect from a press. Some limitations will remain, but we simply have to know where they are. Others are apparent and we need just a bit of effort to take them away.
Which elements of a press are responsible for it’s stability of quality? Yes, operator has abilities to impact many factors of printing press imaging.
During training we will focus on subjects like: colour space, basic colours, gamut and it’s change, special colours, press + paper calibration, optical density, digital workflow, influence of lightning conditions, densitometric and spectral calibration, multitone image printing, ISO and Fogra standards, metamerism, screening and many others.
I also conduct dedicated colour cources for HP Indigo ser.2, ser.3 and ser.4, DFE, Ink Mixing Station operation and working with special inks.
Suggested time for training is 2-3 days in possible 1 day parts. Before training I’d like to be informed about your expectations and CMS policy in print house. Introduction part will be a bit more theoretical with looking at prints and it will take whole day. Next days will be in front of a press.
printing
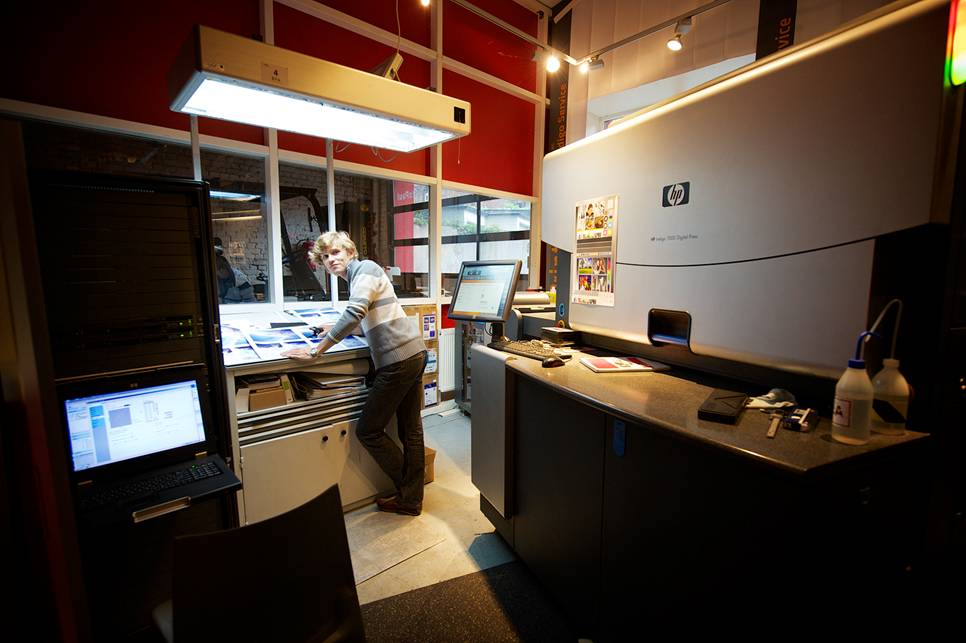
Job comes out on our press screen, we insert paper, press „print“ button and proudly collect prints. And this is exactly what I wish to all of you.
But as experience shows, I got used to certain modifications. Starting with densitometric calibration parameters, fixing geometry, inconstant coverage, adjusting special inks parameters and their selection, screening modification or choosing tools for digital image manipulation inside a press. And yes, at some point I even push „print“ and also there are time I look at print with unhidden pride. Although most likely I’ll find some places to put the quality bar a bit higher.
Oh, but maybe you’re looking for workflow stability and decrease production or tooling time? Maybe it will be repeatable print and made in the shortest possible time? In that case we should refer to automation processes and their proper configuration. But there will come time when new type of job, new challenge will show – it’s worth knowing where to look for solutions. It’s definitely training performed on equipment that you’re using every day.
During course we will talk about: calibration, screening, workflow, job insertion, sharpening, screening angles, linature, full coverage, ink order, colour overlapping, optical density, stability throughout sheet / web, banding, Moiré effect, adhesion and many others.
Suggested time for training is 1-2 days. All time will be spent in front of the press but white boar for visualisation will also be useful.